• HORMIGÓN EN MASA (HM): Se consideran elementos estructurales de hormigón en masa los construidos con hormigón sin armaduras y los que tienen armaduras sólo para reducir los efectos de la fisuración, generalmente en forma de mallas junto a los paramentos. Según la EHE-08, la mínima resistencia para este tipo de hormigón es 20 N/mm2.
• HORMIGÓN ARMADO (HA): Es el utilizado en elementos estructurales que contienen hormigones con armaduras pasivas, como son cimentaciones, pilares, forjados, etc.
• HORMIGÓN PRETENSADO (HP): Es el hormigón utilizado en elementos estructurales con armaduras activas, que comprimen el hormigón y le permiten aumentar su resistencia a tracción, por ejemplo, para tableros de puentes, vigas, viguetas, etc.
• HORMIGÓN IMPRESO O PAVIMENTO IMPRESO: Hormigón en masa en el que se trata la superficie con un molde, dándole diferentes estampados, texturas o productos propios de dicho hormigón (pigmentos, resinas, etc.), simulando a pizarra, piedra, adoquín o baldosa.
• PAVIMENTOS DE HORMIGÓN (HORMIGÓN PULIDO): Hormigón en el que se trata la superficie con un mortero seco (cemento-cuarzo, cemento-corindón, etc.) para posteriormente fratasarlo o pulirlo con helicópteros hasta conseguir una gran dureza en superficie que le confiere altas prestaciones para la durabilidad superficial del mismo.
Se utiliza normalmente para soleras que van a estar expuestas a tracciones superficiales.
• HORMIGÓN FLEXOTRACCION (HF): Hormigón utilizado para pavimentos y firmes de carreteras, puertos, aeropuertos, y otras zonas con elevado paso de vehículos, así como para la reparación de los mismos. Su resistencia está establecida en el PG-3; en función del tipo de tránsito que vaya a soportar dicho pavimento será HF-3.5, HF-4.0 Y HF-4.5.
• HORMIGÓN COLOREADO (HORMIGÓN PIGMENTADO): Hormigón al que se le añaden pigmentos para darle color. De esta forma el hormigón pasa de ser color gris a adquirir otra tonalidad dependiendo del pigmento.
• HORMIGÓN POROSO (HORMIGÓN DRENANTE): Hormigón especialmente indicado para lugares donde se necesita un gran drenaje. Facilita una gran disipación del agua en superficie y previene la existencia de “charcos” en los pavimentos.
• HORMIGÓN CON ADICIÓN DE FIBRAS: Hay muchos tipos de fibras que se adicionan al hormigón, siendo las más comunes las de polipropileno, las de acero y las de fibra de vidrio. Cada tipo de fibra aporta al hormigón unos atributos diferentes, que mejoran sus propiedades en estado “semiplástico” y/o en estado endurecido. En general, excepto las de polipropileno no estructurales, mejoran significativamente la resistencia a flexotracción y a cizalla. Todas en general, actúan en estado “semiplástico” haciendo que las soleras reduzcan significativamente sus probabilidades de fisuración.
• HORMIGONES ALIGERADOS: Hay dos formas de fabricar hormigones y/o morteros aligerados:
• Con áridos aligerados, pudiendo llegar a distintas densidades, desde 550 kg/m3, hasta 2000 kg/m3. Pudiendo utilizarse desde rellenos hasta hormigones ligeros estructurales, con resistencias hasta de 50 MPa.
• Con aditivos espumantes, ocluyendo una cantidad de aire de hasta un 30%. Se utilizan como relleno. Con resistencias aproximadas de 2 MPa, con densidades desde 800 a 1500 Kg/m3.
• MORTEROS POR DOSIFICACIÓN: Se clasifican según su contenido de cemento por metro cúbico. Normalmente se preparan con las arenas adecuadas según su uso. Se venden en consistencias secas o semisecas. Este tipo de morteros se utilizan como rellenos y sobre los mismos se suele colocar solados.
• MORTEROS PARA ALBAÑILERÍA: Normalmente se fabrican dos, uno para tabicar y otro para enfoscar, ambos estabilizados entre 24 y 48 horas.
• MORTEROS AUTONIVELANTES: Se utilizan como relleno para funcionar como soleras niveladas y recepcionar los distintos acabados finales (plaquetas, tarima flotante, parqué, etc.).
• MATERIALES TRATADOS CON CEMENTO (SUELOCEMENTO Y GRAVACEMENTO)
Es la mezcla homogénea, en las proporciones adecuadas de material granular, cemento, agua y, eventualmente, aditivos, realizada en central, que convenientemente compactada, se utiliza como capa estructural en firmes de carretera. Dependiendo del material granular utilizado obtendremos suelocemento o gravacemento.
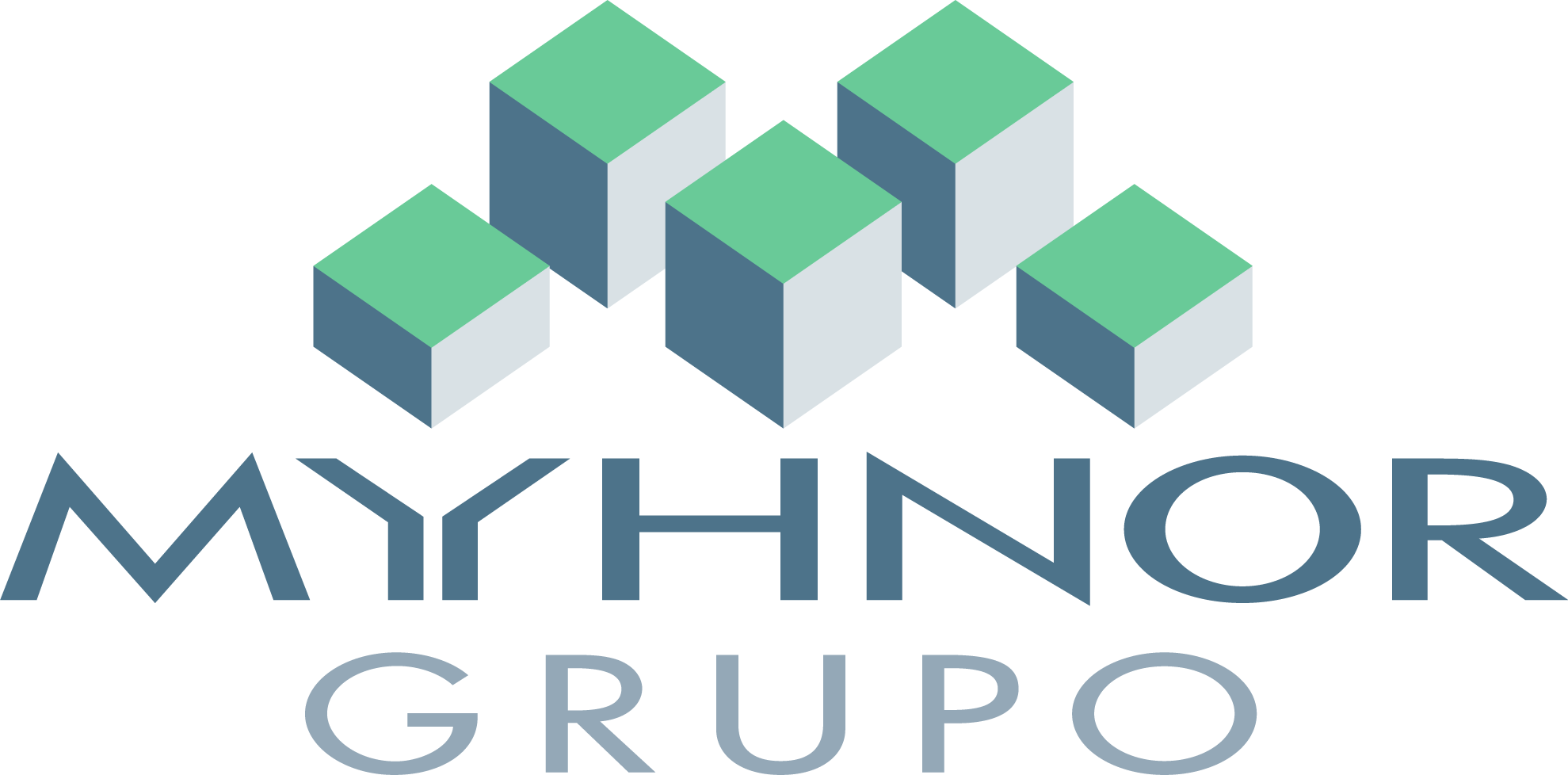